Mesh by Material
mesh-by-material
Darby specializes in stocking many of the standard or market grades of aluminum in alloy 5052. Alloys 1350, 5056 and 6061 are largely considered special order items in aluminum wire mesh. There are times that these aluminum alloys are on the floor or can be readily manufactured. /Asset/aluminum.jpg
Bronze woven wire mesh is superior to brass wire mesh in resistance to atmospheric corrosion, which is a major reason why bronze mesh usage spans from various marine and military applications to commercial and residential insect screen. For the industrial user of wire cloth, bronze wire mesh is harder and less malleable compared to a similar copper woven wire mesh, and as a result, it is commonly used in separation and filtration applications.
Bronze wire mesh has a brownish-red color, and this industrial product is increasingly popular for use in architectural, decorative and artistic applications. /Asset/bronze.jpg
Fencing, caging & enclosures
Farm, garden & agricultural use
Window & safety guards
Archeological use
Building & construction projects
Infill panels
High security applications
Landscaping & gabions
Wall & stone retention
Greenhouse use
Particle separation
General industrial use
Galvanizing can occur either before or after wire mesh is manufactured - both in woven form or welded form. Galvanized before woven wire mesh or galvanized before welded wire mesh indicates the individual wires, themselves, used to manufacture the mesh have been galvanized before the mesh is woven or welded. Depending on the mesh/opening size and diameter wire, this is usually the less expensive option, especially if custom manufacturing is required.
Galvanized after woven and galvanized after welded wire mesh is exactly as it sounds. The material is manufactured, normally in carbon or plain steel, and is often placed in a galvanizing tank, thereby making this a galvanized after woven or welded specification. Generally speaking, this option is more expensive, depending on availability and other variables, but does offer a higher level of corrosion resistance. This added level of corrosion resistance is most noticeable at the joint or intersection of galvanized after welded wire mesh specification.
One of the main benefits of a galvanized wire mesh, especially a galvanized welded specification, is that it tends to offer a wide variety of opening sizes and diameter wires. For instance, mesh opening sizes, such as 4" x 4", 2" x 2", 1" x 1" and 1/2" x 1/2", tend to be readily available from stock in a handful of popularly requested diameter wires.
Due to its attractive price point and its corrosion resistance, galvanized wire mesh is very popular among industrial users of wire mesh. Usually, galvanized wire mesh is specified in applications where relatively large opening sizes are needed. Keep in mind that galvanizing a relatively fine mesh, after it is woven, is likely to clog the openings rendering it unusable in numerous applications. It is for this reason that, usually, a 10 x 10 mesh and finer will be manufactured as a galvanized before woven item.
Darby also stocks and distributes a wide array of vinyl coated welded wire mesh specification. Please contact us for more information. /Asset/galvanized.jpg
In the wire mesh industry, Monel 400® wire is drawn to specific diameter wires and woven to certain specifications. Monel woven wire mesh is commonly used in high performance applications, aerospace, chemical and hydrocarbon processing equipment, as well as in valves, pumps, shafts, fittings and heat exchangers. With a few exceptions, non-industrial users rarely opt for Monel wire cloth due to its high cost and resemblance to stainless steel.
Darby maintains one of the industry's largest and most expansive inventories of Monel 400® wire mesh - particularly in many of the standard or market grades. This inventory advantage allows us to ship stocked material out very quickly. Darby also provides custom manufactured Monel 400® wire mesh. Please contact us with your specific requirements. /Asset/monel.jpg
Aside from stainless steel’s corrosion resistance and clean look, another benefit of selecting a stainless steel welded wire mesh is that because the wires are physically welded at each intersection, the mesh will remain intact and rigid. Strong and consistent welds make stainless steel welded wire mesh an ideal option for general industrial use because welded mesh can be cut down to smaller sizes, like rectangles, squares or discs, without fraying, which can occur when fabricating with a woven mesh.
Like virtually all wire mesh and wire cloth, stainless steel welded wire mesh lends itself for use in architectural, agricultural, commercial and industrial applications. Here are a handful of popular uses for T-304 stainless steel and T-316 stainless steel welded wire mesh:
Another benefit of T-304 stainless steel is heat resistance. T-304 stainless steel displays good oxidation resistance to a temperature of approximately 1600 ºF in intermittent service and to a temperature of 1700 ºF in continuous service. T-304 stainless steel is also excellent for fabrication purposes - it can be formed and cut to size with appropriate tools and machinery. It can also be welded, using most common welding techniques, and it is virtually non-magnetic in the annealed condition. From a cost standpoint, it is usually the most attractively priced of most readily available stainless steel mesh alloys in the industry, especially when taking into consideration its lifecycle.
Darby maintains one of the most expansive inventories of T-304 stainless steel wire mesh, so it is no surprise that when a specific opening size (or mesh count/diameter wire) is needed, T-304 stainless steel is selected. Darby stocks virtually every standard or market grade as well as many of the non-standard specifications, including heavy duty specifications, bolting grades and milling grades. Often referred to 18-8 due to its Chromium-Nickel chemical composition, T-304 stainless steel is available in both woven and welded constructions - both from stock and through custom manufacturing. /Asset/t304-stainless-steel.jpg
T-316 stainless steel has excellent corrosion resistance, and in particular, performs well in its ability to resist pitting and crevice corrosion in warm chloride environments. The inclusion of molybdenum (Mo) is a major factor for the improved corrosion resistance versus a T-304 stainless steel counterpart.
While T-304 stainless steel wire mesh is generally more popular and more readily available in a wide array of specifications, T-316 stainless steel wire mesh is often used and found in the industries highlighted below:
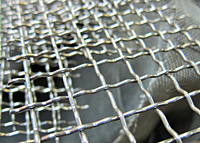
Aluminum Woven Wire Mesh
Lightweight and corrosion resistant in most normal environments, aluminum woven wire mesh is often used in a wide range of industrial applications where separation, filtration or ventilation may be required. Aluminum mesh is also popular in the aerospace, agricultural, architectural, automotive, construction, electronic, food and marine industries.Darby specializes in stocking many of the standard or market grades of aluminum in alloy 5052. Alloys 1350, 5056 and 6061 are largely considered special order items in aluminum wire mesh. There are times that these aluminum alloys are on the floor or can be readily manufactured. /Asset/aluminum.jpg
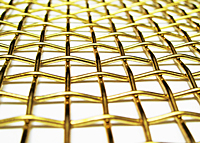
Brass Woven Wire Mesh
Brass woven wire mesh is comprised of copper and zinc. A chemical composition of 65% Copper - 35% Zinc (a.k.a., 270 Yellow Brass) is recognized as the standard for stocked wire mesh in the industry. 70% Copper - 30% Zinc (a.k.a., 260 High Brass) is typically reserved for custom manufacturing. The presence of zinc in brass wire mesh is important because it provides added abrasion resistance and allows for higher tensile strengths. Because brass mesh is primarily composed of copper, it maintains many of copper's unique characteristics, namely softness, malleability and resistance to certain acids.Brass wire mesh is used in architectural, decorative, and of course, industrial applications. Here are a handful of common uses and industries that use brass woven wire mesh:
- Aerospace
- Marine use
- High end infill panels
- Room separation & dividers
- Unique artistic designs
- Decorative lamp shades
- Decorative signage
- RF amplification
- Metal artisans
- Ceiling panels
- Air & liquid filtration
- Fireplace screens
- Chemical processing & diffusion
- Gutter guards
- Cabinet screens
- Metal castings
- Power generation
- Oil strainers
- Plumbing Screens
- Soffit screen
- Air Vents
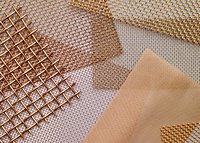
Bronze Woven Wire Mesh
Bronze is an alloy that consists primarily of copper, and thus, it exhibits many of the same characteristics of copper, like malleability, durability and ductility. In the wire mesh industry, commercial bronze wire mesh is the alloy commonly available from stock or through custom manufacturing. Typically, commercial bronze wire mesh has a material chemical composition of: 90% Copper, 10% Zinc.Bronze woven wire mesh is superior to brass wire mesh in resistance to atmospheric corrosion, which is a major reason why bronze mesh usage spans from various marine and military applications to commercial and residential insect screen. For the industrial user of wire cloth, bronze wire mesh is harder and less malleable compared to a similar copper woven wire mesh, and as a result, it is commonly used in separation and filtration applications.
Bronze wire mesh has a brownish-red color, and this industrial product is increasingly popular for use in architectural, decorative and artistic applications. /Asset/bronze.jpg
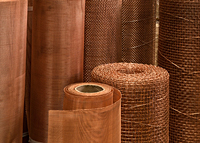
Copper Woven Wire Mesh
Copper wire mesh is ductile, malleable and has high thermal and electrical conductivity. Because of these unique characteristics, it is often used as RFI shielding, in Faraday Cages, in roofing, in HVAC and in countless electrical-based applications. Without a doubt, copper wire mesh is critical to many industries, and it is often at the center of technological advancements in a broad range of fields. Over the past few years, customers have selected various copper mesh specifications for use in:- Energy storage
- Electric heaters
- Pest control fumigation
- Tactical military shelters & modular containers
- Robotics & power automation
- Gamma irradiators
- Health, body and mind enrichment
- Space program initiatives (NASA)
- Metalsmithing & bookbinding
- Air & liquid filtration and separation
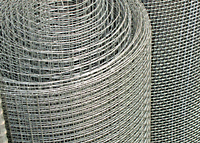
Galvanized Wire Mesh
Galvanized is not a metal or alloy; it is a process in which a protective zinc coating is applied to steel to prevent rusting. In the wire mesh industry, however, it is often treated as a separate category because of its wide spread use in all types of applications. Some of the more popular uses and applications of galvanized wire mesh is listed below:Fencing, caging & enclosures
Farm, garden & agricultural use
Window & safety guards
Archeological use
Building & construction projects
Infill panels
High security applications
Landscaping & gabions
Wall & stone retention
Greenhouse use
Particle separation
General industrial use
Galvanizing can occur either before or after wire mesh is manufactured - both in woven form or welded form. Galvanized before woven wire mesh or galvanized before welded wire mesh indicates the individual wires, themselves, used to manufacture the mesh have been galvanized before the mesh is woven or welded. Depending on the mesh/opening size and diameter wire, this is usually the less expensive option, especially if custom manufacturing is required.
Galvanized after woven and galvanized after welded wire mesh is exactly as it sounds. The material is manufactured, normally in carbon or plain steel, and is often placed in a galvanizing tank, thereby making this a galvanized after woven or welded specification. Generally speaking, this option is more expensive, depending on availability and other variables, but does offer a higher level of corrosion resistance. This added level of corrosion resistance is most noticeable at the joint or intersection of galvanized after welded wire mesh specification.
One of the main benefits of a galvanized wire mesh, especially a galvanized welded specification, is that it tends to offer a wide variety of opening sizes and diameter wires. For instance, mesh opening sizes, such as 4" x 4", 2" x 2", 1" x 1" and 1/2" x 1/2", tend to be readily available from stock in a handful of popularly requested diameter wires.
Due to its attractive price point and its corrosion resistance, galvanized wire mesh is very popular among industrial users of wire mesh. Usually, galvanized wire mesh is specified in applications where relatively large opening sizes are needed. Keep in mind that galvanizing a relatively fine mesh, after it is woven, is likely to clog the openings rendering it unusable in numerous applications. It is for this reason that, usually, a 10 x 10 mesh and finer will be manufactured as a galvanized before woven item.
Darby also stocks and distributes a wide array of vinyl coated welded wire mesh specification. Please contact us for more information. /Asset/galvanized.jpg
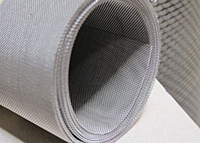
Monel Woven Wire Mesh
Monel 400® (International Nickel Co.) is a uniquely strong and durable material comprised primarily of Copper and Nickel. As a copper-nickel alloy, Monel 400® exhibits high strength and excellent corrosion resistance in a wide range of media, including sea water, as well as acidic and alkaline environments. Monel wire mesh specifications are often requested by naval shipyards and companies that specialize in marine technologies due to these characteristics.In the wire mesh industry, Monel 400® wire is drawn to specific diameter wires and woven to certain specifications. Monel woven wire mesh is commonly used in high performance applications, aerospace, chemical and hydrocarbon processing equipment, as well as in valves, pumps, shafts, fittings and heat exchangers. With a few exceptions, non-industrial users rarely opt for Monel wire cloth due to its high cost and resemblance to stainless steel.
Darby maintains one of the industry's largest and most expansive inventories of Monel 400® wire mesh - particularly in many of the standard or market grades. This inventory advantage allows us to ship stocked material out very quickly. Darby also provides custom manufactured Monel 400® wire mesh. Please contact us with your specific requirements. /Asset/monel.jpg
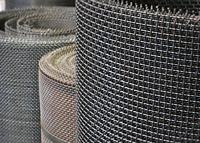
Plain Steel Wire Mesh
In the wire mesh industry, plain steel - or carbon steel, as it sometimes referred to - is a very popular metal that is commonly manufactured in both woven and welded wire mesh specifications. It is comprised primarily of iron (Fe) with a small amount of carbon (C). It is a relatively low cost option that is versatile and widespread in its use. Some of the industries and uses for plain steel wire mesh are as follows:- Caging & enclosures
- Infill panels
- Separation & filtration
- Window guards
- Shaker screens
- Cabinets & wine lockers
- Grill & radiator covers
- Farm & agricultural use
- Oil strainers
- Filtration discs
- Fireplace screen
- Furniture use
- Architectural applications
- Machine & equipment guards
- Hydraulic & fuel industries
- Fan guards
- Decorative use
- Mining industry
- Heat treating
- Building & construction
- Coal industry
- Artistic applications
- Wall coverings
- Security & prison
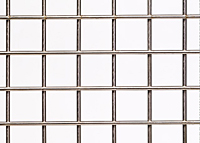
Stainless Steel Welded Wire Mesh
Stainless steel welded wire mesh is an extremely popular and versatile item that many different customers use for many different applications. Darby specializes in supplying high quality stainless steel welded wire mesh, available in both T-304 stainless steel and T-316 stainless steel. Stainless steel welded wire mesh is corrosion resistant, uniform in appearance and available from stock or through custom manufacturing.Aside from stainless steel’s corrosion resistance and clean look, another benefit of selecting a stainless steel welded wire mesh is that because the wires are physically welded at each intersection, the mesh will remain intact and rigid. Strong and consistent welds make stainless steel welded wire mesh an ideal option for general industrial use because welded mesh can be cut down to smaller sizes, like rectangles, squares or discs, without fraying, which can occur when fabricating with a woven mesh.
Like virtually all wire mesh and wire cloth, stainless steel welded wire mesh lends itself for use in architectural, agricultural, commercial and industrial applications. Here are a handful of popular uses for T-304 stainless steel and T-316 stainless steel welded wire mesh:
- Infill panel & railing systems
- Industrial fan & machine guards
- Security enclosures
- Animal retention (cages)
- Small critter control
- Decorative signage
- Room dividers
- Wall cladding
- Ceiling panels
- Air vents & soffit screens
- Basket fabrication
- Food applications
- Racking & storage
- Aviary & bird screen
- Industrial separation
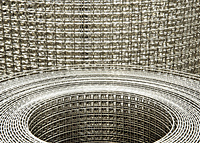
T-304 Stainless Steel Mesh
T-304 stainless steel is the most widely available of all stainless steels in the wire mesh industry. Aside from the countless combinations of mesh opening sizes and diameter wire available both from stock and through manufacturing, T-304 stainless steel exhibits many benefits and is largely considered the standard of the industry. T-304 stainless steel has excellent corrosion resistance in a wide range of environments and is used in a wide range of applications.Another benefit of T-304 stainless steel is heat resistance. T-304 stainless steel displays good oxidation resistance to a temperature of approximately 1600 ºF in intermittent service and to a temperature of 1700 ºF in continuous service. T-304 stainless steel is also excellent for fabrication purposes - it can be formed and cut to size with appropriate tools and machinery. It can also be welded, using most common welding techniques, and it is virtually non-magnetic in the annealed condition. From a cost standpoint, it is usually the most attractively priced of most readily available stainless steel mesh alloys in the industry, especially when taking into consideration its lifecycle.
Darby maintains one of the most expansive inventories of T-304 stainless steel wire mesh, so it is no surprise that when a specific opening size (or mesh count/diameter wire) is needed, T-304 stainless steel is selected. Darby stocks virtually every standard or market grade as well as many of the non-standard specifications, including heavy duty specifications, bolting grades and milling grades. Often referred to 18-8 due to its Chromium-Nickel chemical composition, T-304 stainless steel is available in both woven and welded constructions - both from stock and through custom manufacturing. /Asset/t304-stainless-steel.jpg
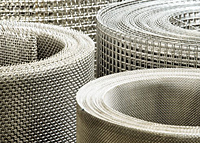
T-316 Stainless Steel Mesh
T-316 stainless steel is recognized as the second most widely available of all stainless steels in the wire mesh industry. T-316 stainless steel wire mesh is typically considered an alternative grade to T-304 stainless steel wire mesh and preferred in certain circumstances. Particularly, in marine environments and in applications requiring heavy welding, T-316 stainless steel is commonly specified due to its many benefits.T-316 stainless steel has excellent corrosion resistance, and in particular, performs well in its ability to resist pitting and crevice corrosion in warm chloride environments. The inclusion of molybdenum (Mo) is a major factor for the improved corrosion resistance versus a T-304 stainless steel counterpart.
While T-304 stainless steel wire mesh is generally more popular and more readily available in a wide array of specifications, T-316 stainless steel wire mesh is often used and found in the industries highlighted below:
- Marine technologies
- Pharmaceuticals
- Chemical processing
- Food preparation & processing
- Rubber, plastic machinery
- Boat & yacht fittings
- Scientific & laboratory use
- Automotive
- Refinery & oil field
- Aerospace
- Particle separation
- General industrial use
All Major Credit Cards Accepted
Connect with Darby